Written by
Eileen Reilly, CEO, Global Train Services, LLC
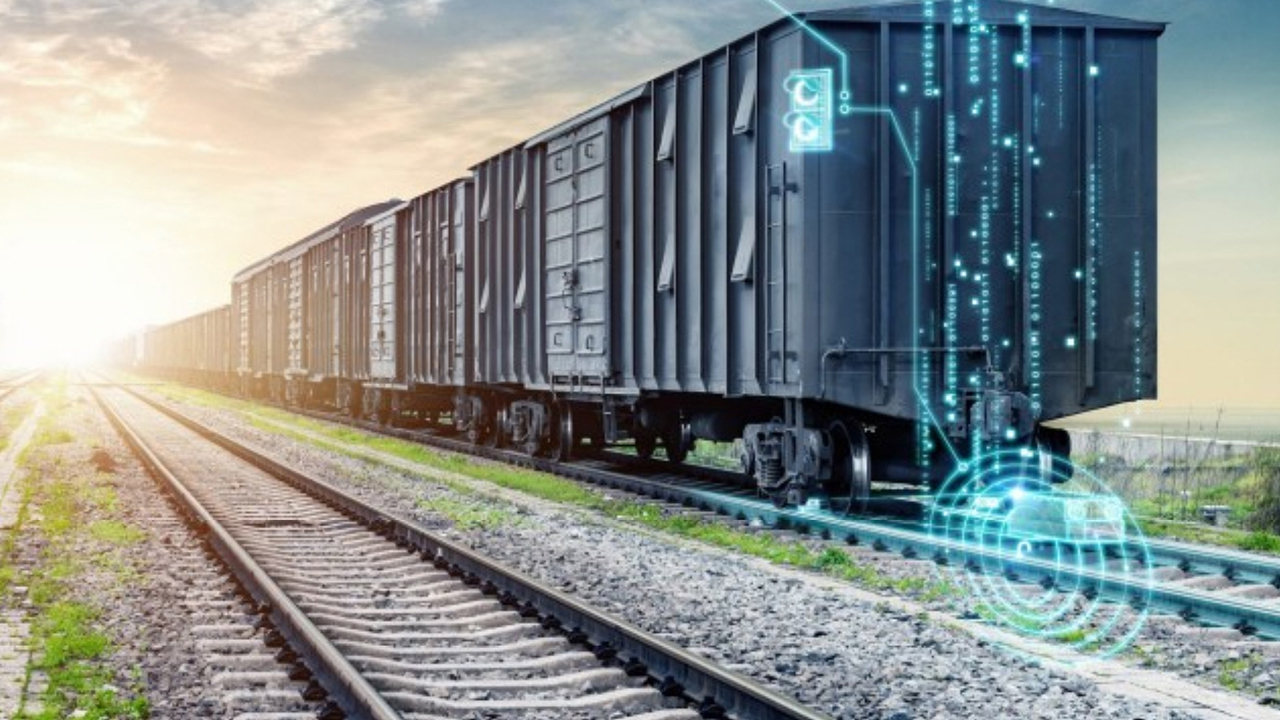
RAILWAY AGE, DECEMBER 2020 ISSUE (updated Jan. 4, 2021): Let’s get moving planning and implementing the technology to achieve the business benefits envisioned when the first PTC systems were being developed.
The National Transportation Safety Board (NTSB) made its first recommendation calling for automatic train control in 1970; 20 years later in 1990, the need for a safety redundancy system on railroads still existed. Positive Train Separation (which was renamed Positive Train Control in 2001) was first placed on the NTSB Most Wanted List that year, and continues with the 2019-2020 Most Wanted List, as number four: “Fully Implement PTC.”
To set the stage, here is some background on PTC: In 2008, Congress passed and the President signed the Rail Safety Improvement Act of 2008 requiring PTC systems to be fully implemented by Dec. 31, 2015, on freight railroad lines with hazmat traffic and/or with regularly scheduled intercity or commuter rail passenger service. The federally mandated PTC systems use communication-based and processor-based train control technology to reliably and functionally prevent train-to-train collisions, overspeed derailments, incursions into established work zone limits, and movements of trains through switches in the wrong position. In October 2015, Congress extended the deadline for full implementation until Dec. 31, 2020, with a Dec. 31, 2018 interim deadline that required the Federal Railroad Administration (FRA) to approve any railroad’s request for an “alternative schedule and sequence” by the final deadline.
The final deadline has been met. In the Dec. 29, 2020 on line article, 100% PTC: An ‘Unprecedented Undertaking,’ Railway Age reported that PTC is now in operation on all 57,536 required freight and passenger railroad route-miles, ahead of the federal deadline of Dec. 31. The 41 railroads subject to the statutory mandate—comprising all seven Class I’s, Amtrak, 28 commuter railroads, and five short lines/regionals that host intercity or commuter service—plus industry associations, suppliers and other service providers, have worked for more than a decade to reach what FRA called “a landmark achievement” and what FRA Administrator Ronald L. Batory said was an “unprecedented undertaking” for the nearly 100 stakeholders.
Now is the time to start planning and implementing what is next: PTC 2.0. As said by Frank D. Roskind (Positive Train Control Systems Economic Analysis, FRA-2006-0132, Notice No. 1, July 10, 2009, pp. 140-144.), “Some of the costs of PTC implementation, operation and maintenance may be offset by business benefits, especially in the long run, although there is uncertainty regarding the timing and level of those benefits. Economic and technical feasibility of the necessary system refinements and modifications to yield the potential business benefits has not yet been demonstrated.” It is time to achieve those potential business benefits that Roskind documented in his economic analysis and help pay the maintenance costs needed to ensure that PTC systems remain in a state of good repair to provide the safety needed and provide the economic benefits that railroads need to stay competitive in the transportation arena.
PTC systems as implemented have provided most of the safety benefits that were promised, but at a high economic cost and reduction in the train velocity of the U.S. rail network. Further safety improvements need to be implemented, as well as the economic benefits that have been anticipated.
The following description of a PTC system was posted on FRA’s website from 2002 through 2012: “PTC systems are comprised of digital data link communications networks, continuous and accurate positioning systems such as GPS, on-board computers with digitized maps on locomotives and maintenance-of-way equipment, in-cab displays, throttle/brake interfaces on locomotives, wayside interface units at switches and wayside detectors, and control center computers and displays. PTC systems may also interface with tactical and strategic traffic planners, work order reporting systems, and locomotive health reporting systems. PTC systems issue movement authorities to train and maintenance-of-way crews, track the location of the trains and maintenance-of-way vehicles, have the ability to automatically enforce movement authorities, and continually update operating data systems with information on the location of trains, locomotives, cars, and crews. PTC’s remote intervention capability permits the control center to stop a train should the locomotive crew be incapacitated. In addition to providing a greater level of safety and security, PTC systems also enable a railroad to run scheduled operations and provide improved running time, greater running time reliability, higher asset utilization, and greater track capacity. They will assist railroads in measuring and managing costs and in improving energy efficiency.”
“It is time to realize the FRA’s vision
and integrate new and existing
technologies to move to PTC 2.0.”
It is time to realize the FRA’s vision for PTC and integrate new and existing technologies to move to PTC 2.0. The integration with tactical and strategic traffic planners is already under way with some of the Class I railroads, but is still out of reach for many short line and regional railroads. For those railroads that are implementing Precision Scheduled Railroading (PSR), PTC is an enabling technology for PSR that provides an origin-to-destination management view through accurate train locations and speed. Many Class I locomotives are equipped with throttle adjustment recommendations for the crew to manually implement, and others can be controlled by the locomotive automatic throttle control that will adjust the train speed based on the schedule to which the train is to adhere. Trains that are moving at schedule speed use less fuel, and don’t arrive earlier than scheduled, where there is no available arrival track or yard crew to take over the train.
Just as important for the train to arrive when it is scheduled are locomotives positioned properly to go on the next scheduled run, improving asset utilization, and cars are delivered to their customer on-time, to be unloaded/loaded when the customer has a crew available, increasing the car utilization. The PTC communications network including Interoperable Train Control Messaging (ITCM), allows for locomotive health status messages from PTC or other sensors to be sent to the owning railroad on a regular basis, no matter where the PTC train is or what railroad it is operating on. If a train breaks down, the exact location of the train is known so that a maintenance crew can be dispatched to the correct location to remove the train from the main line quickly and reduce the amount of train traffic that needs to be diverted, if possible, impacting train velocity and requiring crews that “go dead on the law” to picked up and replaced at a location other than a scheduled crew-change point.
One technology that needs to be considered is the use of additional satellite arrays and frequency bands provided by the Global Navigation Satellite System (GNSS). While the U.S. GPS system is the most prevalent GNSS, Galileo is a global GNSS owned and operated by the European Union and approved by the Federal Communications Commission (FCC) to be used for critical infrastructure to provide PVT (position, velocity and time). This includes U.S. railroads.
The U.S. began a GPS modernization program, and in 2005, GPS L2C became available. It enabled development of dual- and multi-frequency GNSS receivers to correct for ionospheric group delay, and provide for faster signal acquisition, enhanced reliability and greater operating range with higher effective power than the legacy L1 C/A signal, making it easier to receive a signal under trees and even indoors. The L2C full availability capacity is managed with 24 satellites.
On July 30, 2010, the U.S. government and European Union (EU) and its member states announced the conclusion, after an initial phase of consultations, affirming user interoperability and enhanced performance of combined GPS and Galileo receivers. Galileo reached its full operation capability in 2019. With two GPS bands and Galileo operational, GNSS receivers became multi-constellation, multi-band technology, with advanced interference mitigation. Augmentation options including the highest accuracy option of Real-Time Kinematic (RTK) corrections sent from fixed base station receivers 25 to 40 miles apart reduce the error for roving receivers by eliminating satellite and atmospheric error and providing centimeter accuracy.
The addition of a third satellite constellation would provide additional improvement in availability and reliability over using GPS alone, or GPS and Galileo, with more satellites at a higher latitude orbit for the GNSS receiver to use. Efforts are under way to seek approval for the use of the Russian GLONASS System as part of the PVT solution for PTC. GLONASS will increase availability and reliability if GPS and/or Galileo are down or if there is radio frequency (RF) interference, since it is in a different RF band. GLONASS offers increased accuracy at higher latitudes, in urban canyons or terrain that blocks the open sky, or in tree foliage that obscures the open sky. Security needs to be proven, and methods to monitor and remove, if needed, GLONASS constellation signals from a PVT solution before approval will be granted, and work is under way. Inertial measurement units are integrated with GNSS receivers using Kalman filtering that further provides a high degree of confidence in PVT accuracy that allows for distinguishing between parallel tracks.
Train location is critical to keep trains moving, and increased availability will keep trains from stopping when an invalid GNSS message is received. Safety is increased for trains when a train’s initial location can be established without human input that can be in error, with the potential that a train enters PTC controlled track where it has no movement authority but another train does.
Highly accurate train location and GNSS equipment integrated with an end-of-train (EOT) device allows reverse or backup moves to be protected from train-to-train collisions. The technology can be used to detect if the train in a siding has part of its consist fouling the main line, or if a pull-apart (coupler failure) has occurred, so that actions can be taken for other trains that are going to use the same track segment. The increased location accuracy will allow an overly conservative brake enforcement algorithm to reduce the minimum safety buffer, improving capacity, since the position of an entire consist is now highly accurate.
Once an accurate location is known for a train, the need to use track circuits to determine the block(s) a train is occupying is removed. Track circuits can still be used to determine if a broken rail exists on higher speed lines, or newer acoustical broken rail technology can be deployed, since track circuits will not be used to establish train location. Track circuits may still be used at turnouts to provide for point locking, but the number of track circuits can be dramatically reduced, thus reducing fixed-asset maintenance cost. In “dark territory” where wayside signals are absent and form-based authorities such as track warrants are used to control trains, PTC has been very effective in reducing mistakes caused by the verbal read and repeat cycle, and warns or stops the train as it approaches the end of its movement authority.
Wireless grade crossings with highly accurate, reliable GNSS train location messages will ensure that the time the crossing gates are down directly correlates to train speed, instead of a fixed time based on the worst-case time for a train to approach the crossing. Highway users are less likely to try to “beat” the train, and traffic can continue to move at busy intersections for a longer period of time.
As signaling equipment has developed, there have been many refinements to the fixed-block system. However, by removing fixed blocks and enabling moving-block train control, the distance between trains can vary according to their speed in relation to each other. Each train transmits its identity, location, direction and speed to a safety server that makes the calculations for safe train separation and transmits this to the following train. The communication from the train is continuously updating its location to the safety server and transmits to the following train the locations of the train in front so that braking distance is calculated by the following train and can follow at the appropriate, safe maximum operating speed, with enforced braking curves. Moving-block benefits include increasing the rail line capacity, reducing headways between trains, and reducing wayside signal equipment, which is very expensive to maintain since it is widely distributed along the railroad right-of-way; exposed to variable climate conditions, vandalism and theft; and difficult to troubleshoot on busy track segments where time to get to the trouble spot may be difficult. The need to install new wayside equipment will be reduced and possibly eliminated.
For roadway workers, the FRA vision for PTC has not been achieved yet. The requirement of PTC to reliably and functionally prevent incursions into established work zones without receiving appropriate authority and verification from the dispatcher or roadway worker in charge is still handled by roadway workers giving verbal permission, followed by the train crew acknowledging permission on a cab display screen. After such manual acknowledgement, the train’s display shows maximum authorized speed, even if the speed was reduced due to track work. The process is still prone to human error that should be reduced. Technology needs to be implemented to allow roadway workers to electronically communicate train speed movement authority. If communication is not available between the train and the roadway worker, messages can be relayed through the dispatcher, where an electronic message can be sent that provides speed and authorization to move.
Roadway workers, both inexperienced and seasoned veterans, have deployed on-track equipment on unauthorized tracks, with catastrophic consequences. With advances in PTC, it is now possible with highly accurate GNSS receivers and RTK corrections to ensure that on-track equipment is deployed in the correct location, with alerts and warnings if the wrong location is detected. This same technology can be used to show where trains and other roadway workers are located in their on-track equipment display. All roadway workers and on-track equipment in a shared authority should be protected from exceeding their authority, but also be warned, based on their proximity to each other and to moving trains, that they are too close. The technology exists. It is time to begin implementing this safety-critical function.
Finally, by using highly accurate GNSS devices installed in on-track equipment or hand-held devices to mark the locations of temporary speed restriction boundaries and work zones, electronically transmitting their location to the dispatcher, temporary speed restrictions and work zones issued to the train will be highly accurate, since they would be calculated from the same track database and GNSS receivers used on board. This will allow a train to reduce speed prior to entering a work zone, rather than reducing it within a work zone, or worse, passing the speed restriction location, which can cause a serious incident. This same GNSS receiver and equipment can be used to mark the exact location of any critical features that have been relocated or replaced, following maintenance. Safety is improved for track workers and train crews when the track database remains accurate through the life of the PTC system.
These are only some of the improvements to railroad as well as public safety. The economic benefits can help defray the on-going maintenance of PTC. The railroad industry has done an excellent job completing this first phase of complex and expensive PTC. Now is the time to plan and then implement technology to achieve the business benefits envisioned when the first PTC systems were being developed.
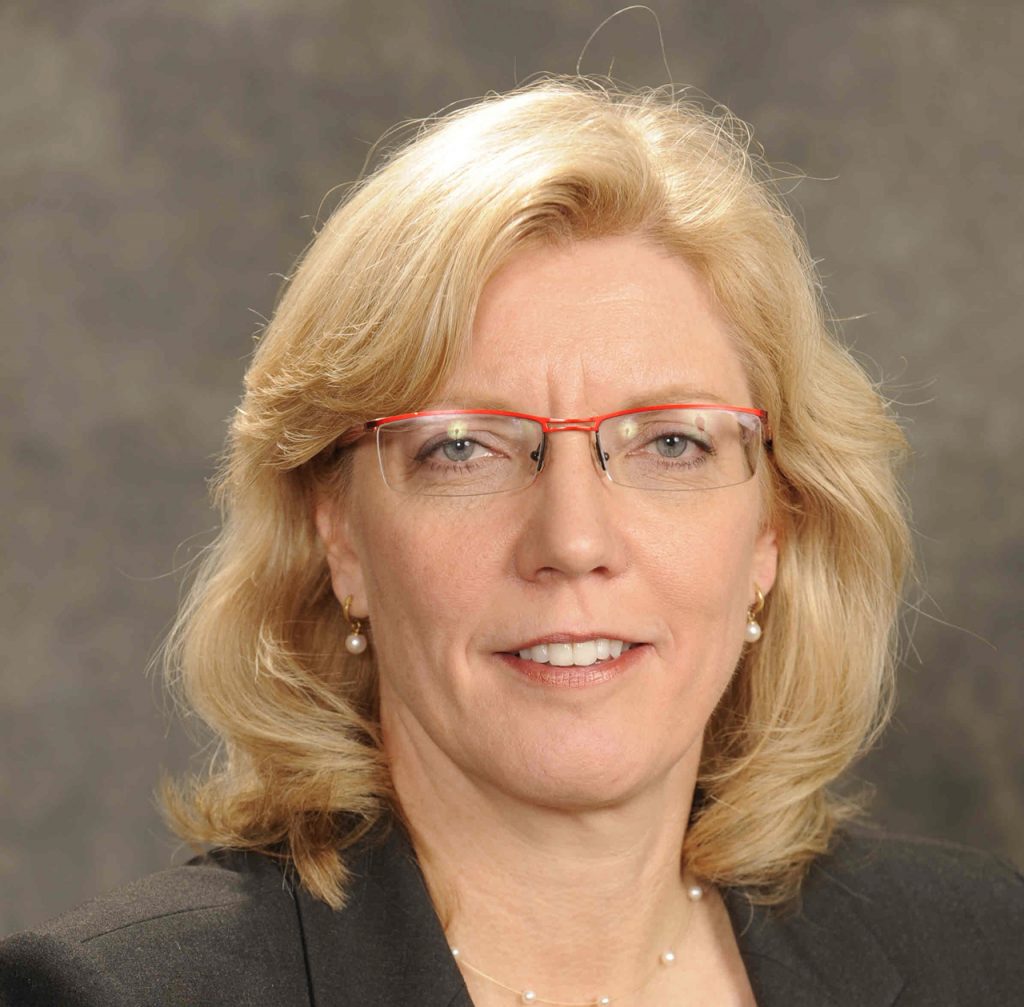
Eileen Reilly is CEO of Global Train Services, LLC (GTS), which she founded in 2018 in response to the growing need for technology experts in the railroad industry. Advanced train control technology is GTS’s specialty, creating software tools to further railroad safety and generate operational efficiencies by leveraging data derived from existing railroad systems. GTS can also provide compliance consultation to railroads working toward meeting full implementation of PTC. GTS is a member of ASLRRA’s Preferred Provider Program, offering PTC implementation, support and grant writing services at a discounted rate through ASLRRA’s Member Discount Program. Reilly was formerly Vice President of Advanced Train Controls at the Alaska Railroad. She has successfully developed, implemented and lobbied for advanced rail safety systems since 1993, with a specific focus on PTC for the past 22 years, while participating as a member of the Railroad Safety Advisory Committee (RSAC) to develop new regulatory standards for the Federal Railroad Administration.