Microdispensing equipment manufacturer nScrypt has achieved 6-axis 3D printing with its new 3Dn-Axis Factory in a Tool (FiT) 3D printer.
Based on the previously released 3Dx-700, the multi-head 3Dn-Axis comes complete with nScrypt’s entire line of specialized toolheads. This includes the SmartPump microdispensing tool, the nFD material extrusion tool, the nMill milling and polishing tool, and the nPnP360 pick and place tool. As such, the comprehensive 3D printer is well suited to complex functional device production, with potential applications in integrated electronics, sensors, and radio frequency communication devices.
Ken Church, nScrypt’s CEO, states, “We are finding that printing only in XYZ just isn’t meeting customer needs. Rather than 3D printing parts, they want to do precision digital manufacturing of finished products in true 3D, such as integrating circuits and electronic components, like sensors, in helmets and other wearables, or in projectiles, drones, or medical devices.”
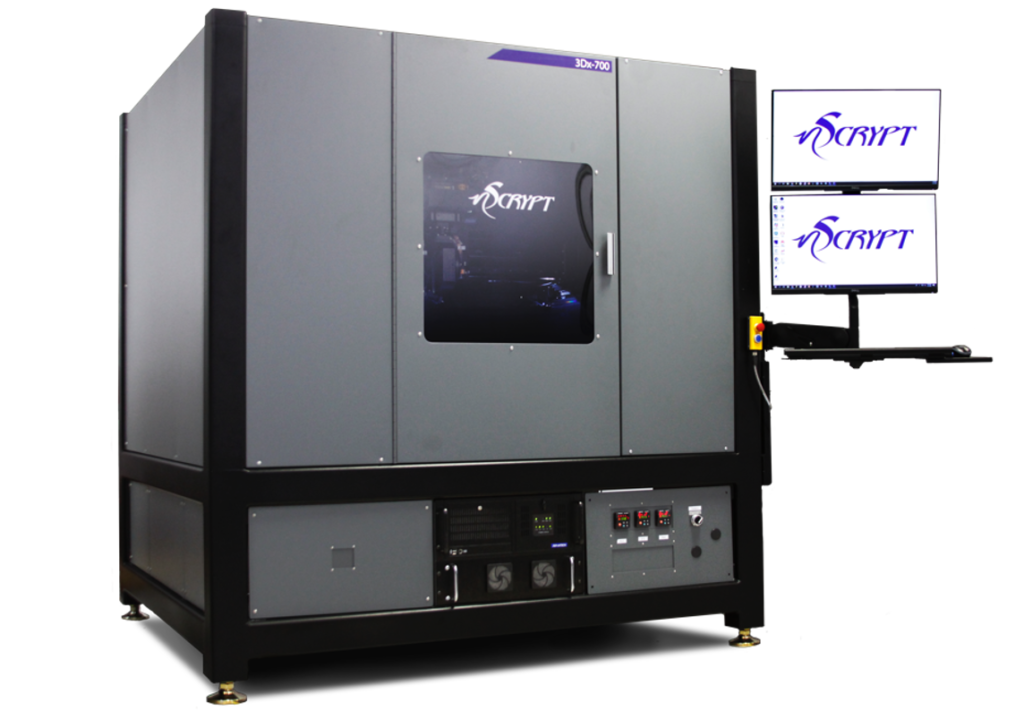
Microdispensing with nScrypt
nScrypt’s extensive range of Factory in a Tool 3D printers includes the 3Dn Series, the 3Dn-DDM Series, and the nRugged system. Each of the machines is compatible with the company’s entire tool head suite, which makes them well suited to electronic device 3D printing.
Using nScrypt’s tool changing system, the FiT 3D printers are able to switch seamlessly between each of the specialized tool heads. In this way, the nFD tool can be used to 3D print the polymer casing of an electronic device; the SmartPump can be used to dispense the conductive traces in silver ink; the pick and place tool can be used to assemble the individual components; and the milling tool can provide users with a high-quality surface finish. The new 3Dn-Axis now allows for all of this in 6 axes.
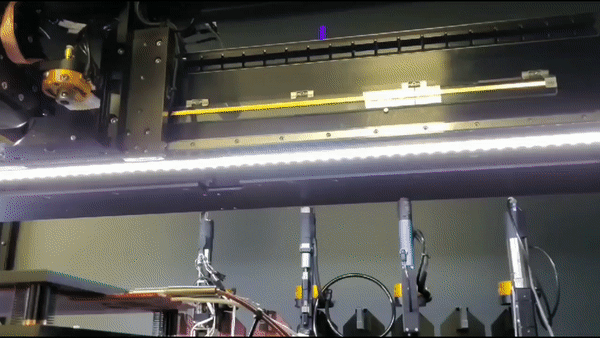
6-axis 3D printing on the 3Dn-Axis
6-axis 3D printing provides users with a new level of geometric control when designing parts. On top of the standard linear XYZ planes, nScrypt’s new FiT system features three additional rotational axes of motion. The RS axis serves to spin the tool head, the RT axis tilts the tool head, and the RR axis spins the print bed.
The additional axes ultimately enable conformal dispensing capabilities, much like a non-planar FFF 3D printer. nScrypt has already demonstrated the system’s printing capabilities via a number of test prints shown below. The image on the left shows a 3D printed polymer part with a secondary STL file wrapped around it. Similarly, the image on the right shows a 3D printed thermoplastic base with a DXF file wrapped around it, which tells the printer to dispense a conductive silver ink pattern into the curved surface.
Church adds, “Our 3Dn-Axis Factory in a Tool solves two problems: the ability to 3D manufacture complete products, like functioning electronic devices, and the ability to do so in true 3D, making complex shapes with integral electronics and fine surface finish. Our new FiT allows our customers to move beyond XYZ 3D printing to true 3D manufacturing.”
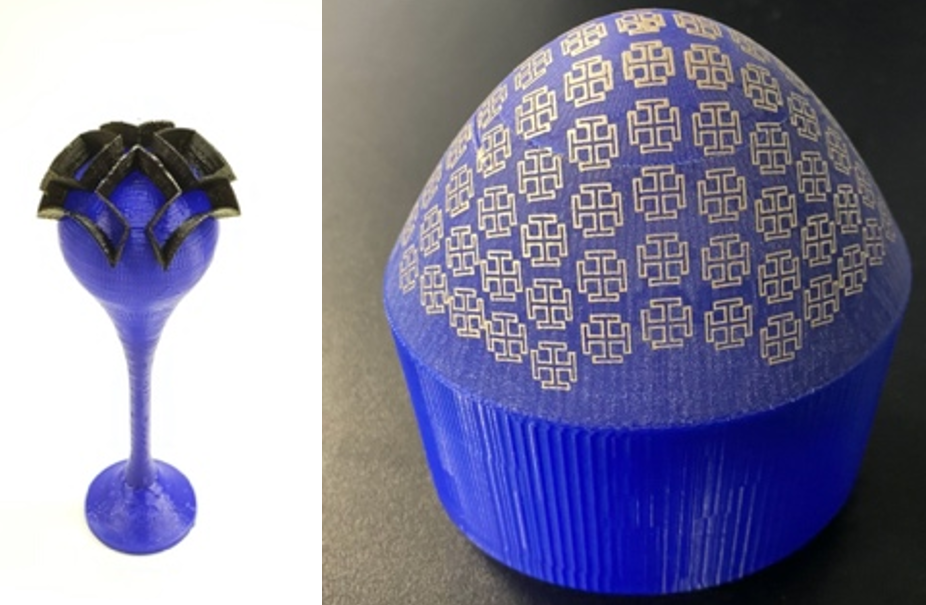
Earlier this year, nScrypt used its FiT 3D printing technology to produce engine parts for automotive R&D firm Larsen Motorsports’ latest dragster. Leveraging the nRugged system, Larsen was able to replace the outdated gaskets on the fuel pumps of its new ‘Gen 6’ jet-powered car, with more durable fabricated seals.
Elsewhere, the nRugged has also previously been demonstrated to the Secretary of the Army, Ryan D. McCarthy, as a potential production tool for the U.S. Army. As suggested by the name, the system is designed for 3D printing in harsh environments, and shows great potential for electronic device or bioactive bandage manufacturing out in the field.
Subscribe to the 3D Printing Industry newsletter for the latest news in additive manufacturing. You can also stay connected by following us on Twitter and liking us on Facebook.
Looking for a career in additive manufacturing? Visit 3D Printing Jobs for a selection of roles in the industry.
Featured image shows the 3Dx-700. Photo via nScrypt.