Additively manufactured electronics (AME) manufacturer Nano Dimension has announced its first 3D printed integrated radiofrequency (RF) circuit has been flown to the International Space Station (ISS) for space effects studies.
Printed on Nano Dimension’s DragonFly LDM system, the RF circuit will transmit data to and from the ISS, providing the project partners with systematic analysis of the RF properties of 3D printed High-Performance Electronic Devices (Hi-PEDs) within the rigors and demands of space.
Nano Dimension collaborated with communications technology firm L3Harris on the two-year project, which ultimately aims to demonstrate the viability of using new technologies such as multi-level and multi-material AMEs for use in space.
“This project has been a significant opportunity to qualify our additive manufacturing technology for space applications by fabricating a fully integrated communications board enabled by the multi-material and multi-layer technology of our DragonFly LDM system,” said Dr. Jaim Nulman, Nano Dimension’s Chief Technology Officer.
“The collaboration with L3Harris has increased the technological readiness of our system towards the TR-9 level, which is the highest technology readiness level that indicates the capability for volume deployment in a LEO environment.”
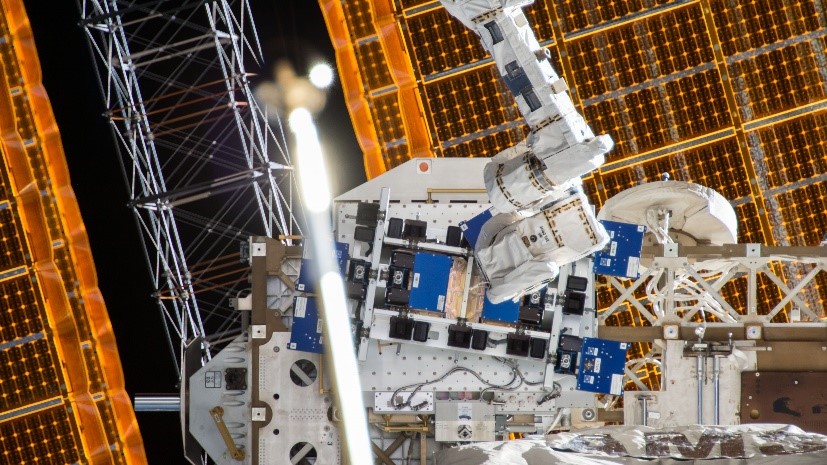
AMEs for space applications
Low Earth Orbit (LEO) refers to a region 1,200 miles above Earth that is home to the ISS and other communications satellites, all of which utilize RF communications systems. Using AME technology to produce lightweight, high-performance electronic devices for use within these RF systems has the potential to yield several advantages, including rapid development time and the ability to create complex shapes and systems unachievable with traditional manufacturing techniques.
Typically, the traditional production of RF circuits is a tedious trial and error process involving multiple design iterations. As such, the development of AMEs for potential space applications is an area that is seeing mounting interest.
In 2017, 3D printed metal and electronics firm Optomec was awarded a NASA Small Business Innovation Research (SBIR) contract to develop its post-processing Adaptive Laser Sintering System (ALSS) and enable electronics 3D printing onto a wider variety of temperature-sensitive substrates for use on the ISS. Elsewhere, Silicon Valley-based startup Space Foundry has been exploring how its plasma 3D printing technology could be applied within the space and electronics industries.
In October last year, Swiss RF component supplier SWISSto12 delivered a large batch of 3D printed waveguide signal interconnects to Thales Alenia Space for use in the Eutelsat KONNECT Very High Throughput Satellite (VHTS) program. Manufactured using 3D printing and electroless plating, the waveguide components saw weight and cost savings alongside enhanced RF performance.
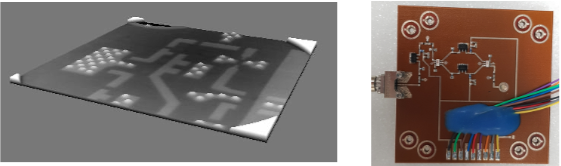
Fabricating the RF circuit
The project between Nano Dimension and L3Harris was issued by the ISS US National Laboratory to test the durability of 3D printed RF circuits in space for potential use in future small satellites.
“Additive manufacturing, or 3D printing, is playing a critical role in advancing the development and applications of small and nano satellites and the overall LEO economy,” said Dr. Arthur Paolella, Senior Scientist in the Space and Airborne Systems segment of L3Harris. “The applications of 3D printing are broad, touching almost every aspect of research, design, and manufacturing.”
Utilizing its experience in RF circuit development for satellites and communications systems, L3Harris designed the RF circuit board and, once printed by Nano Dimension, mounted the component to the exterior of the orbiting laboratory of the MISSE Flight Facility launch module.
Nano Dimension 3D printed the RF board using its DragonFly LDM system which is equipped with the company’s proprietary AME technology. The system features two individual printheads that simultaneously deposit a conductive silver nano-ink for the bulk of a printed circuit’s connections, and a dielectric photopolymer ink, which provides mechanical support, thermal resistance, and electrical insulation for the surrounding structure.
The multi-layer 3D printed communications device, which is 101 x 38 x 3 mm in size, is comprised of an antenna, electronic traces for mounting functional components, and a signal ground plane. According to L3Harris, when compared with a conventionally manufactured counterpart the 3D printed RF circuit displayed a similar transmission performance while delivering reduced costs and a faster time to market.
The device will be tested at three program points – pre-flight, in-flight, and post-flight – and will be exposed to the LEO environment on the ISS for six months before being brought back to Earth for evaluation.
“The major objective of this project is to fly an experiment consisting of an integrated communications circuit fabricated by additive manufacturing and analyze the RF properties of those materials in a space environment,” added Paolella. “The communications system now on the ISS went through extensive testing in order to prepare it for the mission. Nano Dimension’s contribution to this project was extremely important, as their additively manufactured capability is technologically advanced and superior to existing technologies.”
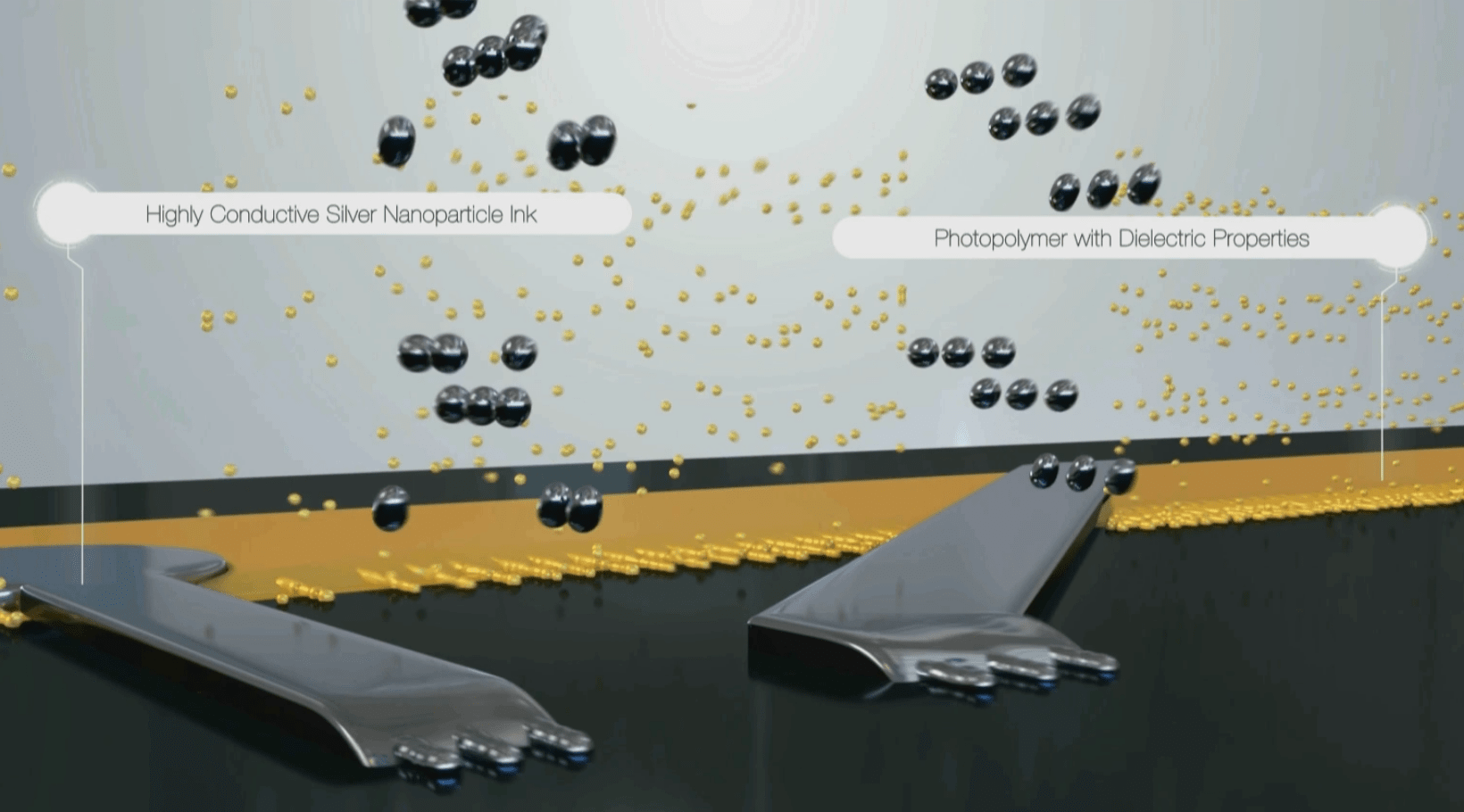
Subscribe to the 3D Printing Industry newsletter for the latest news in additive manufacturing. You can also stay connected by following us on Twitter and liking us on Facebook.
Looking for a career in additive manufacturing? Visit 3D Printing Jobs for a selection of roles in the industry.
Featured image shows Nano Dimension’s First Ever AME RF communications circuit has been sent to the ISS. Photo via Nano Dimension.