Article By : Maurizio Di Paolo Emilio
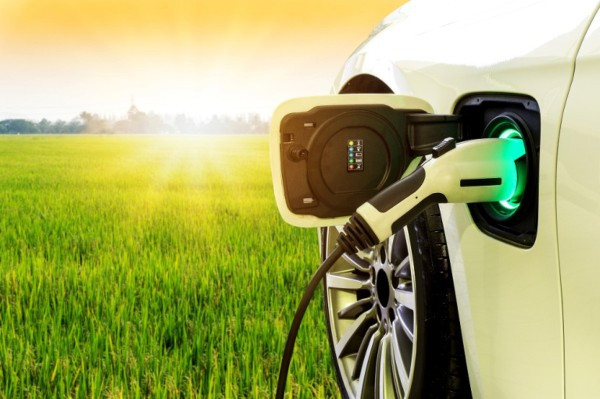
Electronics is at the heart of the automotive industry and will be increasingly so with electric vehicles.
Electronics is at the heart of the automotive industry and will be increasingly so with electric vehicles. The enormous evolution of microelectronics, in particular high-power electronics, has led to a marked increase in infotainment, lighting and sensor applications that require a robust and reliable design. Analysts estimate a turnover of over $80 billion with exponential growth in the coming years. The industry is actively contributing to road safety through the development and evolution of technologies to limit accidents, for example through stability control systems and driver health status.
The advent of smart (intelligent) technologies, starting with the smart grids, has seen an interest towards GPS and the entire IoT ecosystem for supporting vehicles in the reception and transmission of high-speed data. Three main factors make the car attractive for technology: autonomous driving, electric vehicles, and the strong consumer demand for infotainment services. Driverless cars represent the challenge of the near future. The possibility of remotely intervening with programmed electronic systems, reducing the number of road accidents, and thus avoiding dangerous situations, is a reason to bring this challenge to success.
Let’s see how electronics has taken over from mechanics.
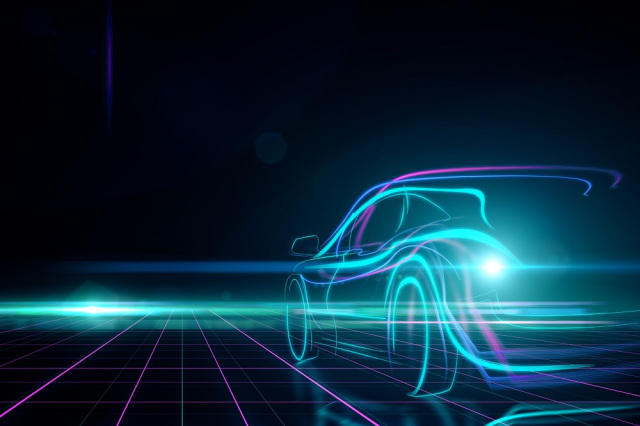
MEMS technology
Although typical applications are airbags and advanced driver assistance systems, the proliferation of sensors such as MEMS-based gyroscopes and accelerometers allows for a range of control solutions that offer greater efficiency. Micro-electromechanical systems (MEMS) technology uses microfabrication techniques to combine the capabilities of microelectronics with the mechanical properties of microsensors. The advantages of these approaches include high efficiency, small size, and low cost. MEMS-based electronic safety systems can ensure compliance with functional safety standards and enable designers to achieve their goals more efficiently. The growing demand for safety and security in the automotive sector is the main driver for the growth of this market. MEMS accelerometers measure accelerations on one, two or three orthogonal axes and are used to identify the inclination or orientation with respect to the acceleration of gravity, as well as to measure vibrations and shocks. Accelerometers are based on the Silicon (Si) semiconductor. The physical principle of measurement essentially consists of a thermal or capacitive approach. The capacitive approach may be more suitable for some applications, such as crash detection and airbag activation. On the other hand, the thermal approach based on the principle of convection of gas molecules heated inside a sealed cavity, is more suitable for electronic stability control (ESC). Capacitive devices exploit the piezoelectric effect or the stress of the crystal structure with accelerating forces that cause mechanical stress transformed into an electrical signal.
MEMS gyroscopes, on the other hand, provide an easy way to measure angular velocity (or rotational motion) and are a popular choice for motion control. They are also used in the consumer sector, on most smartphones. Active suspension employs four sensors in combination with accelerometers and gyroscopes to ensure a stable and regular dynamic behavior for the vehicle. Most gyros are based on a tuning fork configuration with two masses, continuously oscillating in opposite directions. When an angular force is applied, the Coriolis force on each mass acts in the opposite direction, creating a variation in capacity proportional to the angular velocity, which is then converted into an electrical signal. As for the noise, we have an intrinsic noise representing the state of static inertia, that is to say without rotation, vibrations, shocks and in environmental immunity conditions.
Hence, automotive applications for accelerometers mainly include airbags and active suspension, while gyroscopes are used in stability control systems and GPS navigation systems. A gyroscope can be used in cars to activate the electronic stability control (ESC) braking system to prevent accidents, or to activate an airbag when a lean condition or frontal crash occurs. A new MEMS market is emerging with Nano Electro-Mechanical Systems (NEMS). Thanks to their sensitivity, these nano-sized devices are capable of offering very small sensors that can detect stresses and vibrations at the atomic level.
Electromagnetic Compatibility (EMC)
The fast development of the automotive industry and the trend towards autonomous vehicles and ADAS systems continue to drive the need for more sophisticated EMC designs and test scenarios for the automotive industry. Vehicle platforms are becoming increasingly complex with electronic devices that require a reliable operation without affecting safety or the communication infrastructure. The automotive industry and its manufacturers aim to meet a variety of electromagnetic compatibility requirements. For example, two requirements must ensure that electronic devices do not emit electromagnetic interference (EMI) or excessive noise and are immune to noise emitted by other electromagnetic sources.
The new wireless communication paradigms applied to the automotive sector require high-performance electronic systems that operate at high data rates and, therefore, at high frequencies depending on the operating environment. Each of these new subsystems must comply with electromagnetic compatibility standards. Furthermore, signal integrity, as well as transmitted and processed data patterns are critical aspects. The miniaturization of electronic devices is a must and, as a result, manufacturing tolerance can no longer be neglected. Variations in nominal design parameters cause erratic behaviors that negatively affect both EMC and signal integrity. Automotive systems have several radio receivers installed around the car. The IEC Commission has formulated international standards to protect them. The international standard for this electromagnetic noise is formulated as CISPR 25. CISPR 25 is a standard with several test methods. The electromagnetic noise level in the test area shall be at least 6 dB lower than the lowest level being measured. Another test standard is ISO 11452-4 Bulk Current Injection (BCI), which checks if a component is adversely affected by narrowband electromagnetic fields. The test is performed by injecting noise directly in the wiring with a current probe. CISPR 25 contains limits and procedures for measuring radio interference in the frequency range from 150 kHz to 1000 MHz. The standard applies to any electronic/electrical component intended for use on vehicles, trailers, and various devices.
Noise in a vehicle
One of the most important aspect regarding the automotive sector is the combustion phase in the cylinders of endothermic engines. As these motors have been around for many years now, engineers have always been working on design techniques to handle low frequency noise. We will see how, with electric vehicles, the issue to be managed is exactly the opposite: they emit too low noise and we have to create more for safety reason.
Energy saving techniques have helped to produce more environmentally friendly vehicles, but not always providing a less noisy cabin experience. By reducing the number of cylinders with more efficient and more environmentally friendly engines, the frequency of engine noise is reduced. To reduce engine noise, automotive engineers use Active Acoustic Control or Active Noise Control (ANC) to generate noise-canceling signals that are reproduced by speakers in the car’s cabin. Active noise control (ANC) technology uses the vehicle’s audio system to reduce unwanted noise generated by the engine. Active audio sound control is a signal processing methodology that reduces the effective amplitude of the sound to improve the signal-to-noise ratio (SNR), so that unwanted noise is less perceptible. The active noise control methodology is also called ANR (Audio Noise Reduction). ANC or ANR is based on coherent acoustics that aim to accurately replicate the original sound field in all its forms using amplifiers and microphones inside vehicles and digital signal processing (DSP) to cancel noise. In practice, sound can be described as a pressure wave consisting of an amplitude and a phase.
A noise cancellation system consists of an audio device that emits a wave with the same amplitude but a phase shift of 180° (inverted phase, also called anti-phase). The recombination process of the two waves is based on a physical principle called destructive interference. Active noise control is achieved by using mixed-signal circuits or digital signal processing, with a control algorithm to analyze the sound waveform and to generate an anti-phase wave amplified to a transducer. These systems heavily rely on integrated SoC (System-On-a-Chip) equipped with high performance standard CPU and software infrastructure. Real-time processing resources are required to quickly implement and complete feedback control loops, in order to allow the ANC solution to work properly. In a typical automotive system design with three to six microphones, the system meets the needs of a typical passenger compartment by reducing noise in the 30-250Hz range, a spectrum that covers the firing frequencies of a four-cylinder engine.
LED lighting
In the automotive industry, light-emitting diodes (LEDs) are widely used for high beams, brake and position lights, and side and rear turn signals. In an LED driver project, the brightness intensity of the various lighting devices is not the same but depends on their specific function. Therefore, LEDs work at different brightness levels; for example, at maximum brightness for braking and 10% to 25% brightness for rear lights. LED dimming circuits are used to differentiate the brightness level through a pulse width modulation (PWM) driving technique, which modulates the width of the current pulses applied to the LEDs. For outdoor lighting applications, however, it is necessary to provide different brightness levels for the same LED. For example, stop and side lights or low and high beam are defined at two brightness levels. In some cases, the design can satisfy both situations with the same LED by using a suitable driver.
An essential aspect of the lighting control system is the management of the power provided by the integrated circuit (IC) drivers in different configurations, known as buck and buck-boost. The ease of control of the LEDs makes them a smart lighting system.
LED solutions require a constant current to produce uniform brightness. The accuracy of the source, the fluctuations in voltage and other parameters are actually the most relevant design parameters for a correct driver implementation. The vehicle’s power ripples supply must, therefore, be carefully considered. In addition, other requirements that are reflected in the design phase include temperature and humidity, voltage range, electromagnetic compatibility (EMC), as well as the reliability requirements dictated by qualification tests. The high reliability in automotive applications is an indication of the necessary protection circuits, inside the driver IC, against overvoltage, undervoltage, reverse polarity, overcurrent, short circuit and extreme high or low temperatures. Harsh automotive environments require protective circuitry to prevent issues in case of failure. Automotive grade devices are also expected to demonstrate reliable operation over an extended temperature and humidity range and the ability to withstand continuous vibrations.
Gesture recognition
Gesture recognition or gesture detection is the ability of a device to identify a series of movements of the human body in order to apply certain control functions. This electronic technology is based on the aid of a camera that identifies and scans the scene in a 2D or 3D scenario, or through solutions based on the Time-of-Flight (ToF) technique. The latter consists in sending an infrared ray on the target to be analyzed, with consequent reflection of the signal processed by the receiving electronics. The electronics create a kind of map by analyzing the various movements and, through an algorithm, it will respond with the correct action. Other solutions employ ultrasonic signals such as those used in parking sensors.
The goal is to scan the entire image of a scene. The cameras used are made up of a transmitter and a receiver sensor (consisting of a matrix of pixels that collects light from the same region of interest). The vision control algorithm will have to scan the images to analyze the gesture and proceed with recognition. The objective of the sensors is to demodulate the reflected light, measuring the position of each pixel which represents the correlation between transmitted and reflected light. Pixels collect light from various separate parts of a scene. By recombining signals, a reconstructed image is created. All sensor pixels are controlled by a demodulation and a modulation input. Pixel demodulation is synchronous with the modulation of the transmitted light signal.
The conversion of photons (light reflected on the matrix) into electrons of a quantum process is regulated by stochastic functions. In particular, the photon generation rate uses a Poisson distribution. Similarly, the signal of the photons reflected by the target and the relative conversion of the same into electrons within the pixel are also quantum processes with a Poisson distribution. In these cases, not all of the light hitting the pixel is converted into electrons. To check the quality of the system, it is best to measure the quantum efficiency as a function of the wavelength of the light used in the transmission.
The gesture recognition technique also involves the eyes. Suppose you want to start the rear wipers by simply moving your eyes to the rearview mirror or turn on the radio by simply moving your eyes to the dashboard. These are among the many examples and features that the control algorithm shall be able to decode in real time. A key feature is the ability to monitor psycho-physical symptoms that could have negative consequences while driving, such as fatigue. Modern eye tracking systems use infrared (IR) LEDs as a light source and high-resolution cameras to detect reflected light.
LiDAR
The principle behind LiDAR (sometimes also found written Lidar or LIDAR) is quite simple but building a system of this type is not necessarily straightforward. The formula used by engineers to calculate the distance is: distance to the object = (speed of light x time of flight) / 2. The LiDAR measures the flight time used to calculate the distance traveled. The system basically sends high frequency light pulses with wavelengths from about 830 nm to 940 nm and uses a mirror instead of an antenna to scan the laser. This light bounces off a sensor, which interprets the signal and calculates the distance traveled by the light by measuring its diffusion. In this way, LiDAR systems allow autonomous vehicles to detect obstacles or other vehicles.
One of the complicating factors is that the emitted light can be reflected in different directions. When looking at a tree, some photons will be reflected from the branches, but others will continue through and will be reflected from the ground. It is possible, or even probable, that multiple reflections can give rise to a pulse of light. Essentially, it is very similar to radar technology. Both use parameters such as speed, angle, and range. Radar, of course, uses radio waves instead of light. The hardware essentially consists of a transmitter and a receiver and a set of points that identifies a large amount of data from the scanned environment. This creates a dataset that can be transformed by a software application to create 3D images based on a given area.
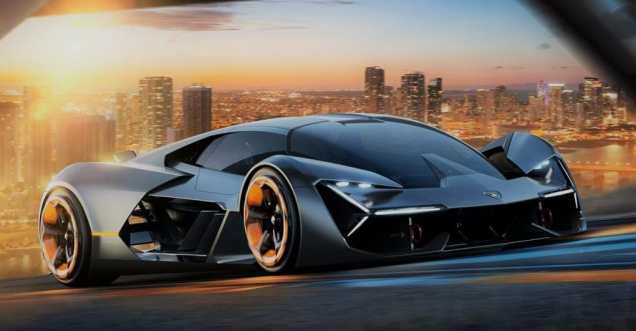
Electric vehicles
At the heart of the global drive towards a more sustainable future are electric vehicles.
Electric vehicles basically use electricity to run the engine. They require DC/DC converters (converters from one direct current to another that is always continuous but with different voltage), typically from high voltage to 12V to power the low voltage electronics; a DC/AC traction inverter for driving electric motors (usually three-phase) and provide power to the wheels, and AC/DC converters for charging vehicle batteries both during braking energy recovery and from residential or high-power (for fast charging) charging stations. Electricity can be generated by the car’s braking system to recharge the battery. This is called “regenerative braking” and consists in converting kinetic energy into electrical energy.
There are three main types of electric vehicles (EV), classified according to the degree of use of electricity as an energy source. BEVs, or battery electric vehicles, PHEVs, plug-in hybrid electric vehicles and HEVs, or hybrid electric vehicles. Battery electric vehicles, also called BEVs, and more frequently called EVs (incorrectly), are fully electric vehicles with rechargeable batteries and without a gasoline engine. Battery electric vehicles store electricity on board with high-capacity battery packs. Their battery power is used to operate the electric motor and all on-board electronics. BEVs do not emit harmful emissions and hazards caused by traditional gasoline vehicles. Electric vehicle (EV) chargers are classified according to how quickly they charge an electric vehicle battery. Plug-in hybrid electric vehicles or PHEVs can recharge the battery via both regenerative braking and through the “connection” to an external power supply source. While “standard” hybrids can (at low speeds) travel about 1-2 miles before the gasoline engine fires, PHEV models can go anywhere from 10-70 km before their gas/gasoline engines give their contribution.
The push by designers in electric and hybrid vehicles to improve energy conversion efficiency is moving towards highly reliable devices in terms of both thermal management and loss reduction. The design parameters are different and concern the power level, the conversion efficiency, the operating temperature in the vehicle transmission system, how easily heat can be dissipated and the system package. The keys to performance in the EV design are the battery and propulsion system. Another aspect to consider is the autonomy of an EV, or the distance that it can travel with a full charge. The popularity of electric and hybrid vehicles has led to new integrated solutions, which make battery management more reliable. Wireless battery management systems (wBMS) or simply non-wireless (BMS) battery management systems are being developed to further improve the safety and reliability of automotive batteries.
The most popular lithium-ion batteries now require special attention because the characteristics of each cell change differently from the other. Therefore, each cell must be handled individually to completely avoid discharge. Obviously, most manufacturers consider the loss of power very dangerous and unacceptable during operation. For this reason, they try to achieve extremely low failure rates. Lithium-ion batteries require special attention when they need to provide reliable operation over a long period. Battery electronics must be able to communicate information from each cell in a battery stack to a central point for processing. In addition, the battery management electronics must maximize the range, duration, safety, and reliability while minimizing costs, size, and weight.
All electric or hybrid vehicles use regenerative braking to charge the battery during deceleration. In addition, solar cells can be used to restore maximum battery charge or to compensate for the quiescent current in the car. In addition to solar energy, other sources available are heat and the piezoelectric effect using mechanical kinetic energy. Some parts of a vehicle become very hot and the difference in temperature can be used to store energy and recharge the battery (thermal energy harvesting). In this scenario, a mesh networking solution such as SmartMesh can eliminate any maintenance related to connectors, cables, and various assemblies. It also allows the implementation of additional features, while providing some scalability.
Energy harvesting used in the automotive sector consists in taking energy from external sources and converting it into electrical current to provide power to any device. The collection of kinetic energy is a universal way to collect energy in the engine compartments, due to the vibration energy that is always present with different amplitudes. Using several conversion principles and an appropriate microelectronic system, this energy can be efficiently converted into an electric current. However, the performance of energy harvesting strongly depends on its ability to adapt to the environmental source. Recent advances in the development of ultra-low-power microcontrollers have resulted in devices that offer unprecedented levels of integration with respect to the power required to operate. Energy harvesting from sources such as heat, light, sound and vibrations could have a significant impact on economic and environmental factors, reducing costs and generating new sensor technologies for the automotive industry.
We have seen that batteries are at the heart of any electric vehicle. The adoption of batteries in electric vehicles has oriented electronic design towards a new generation of electric charge monitoring devices. Lithium-ion battery cells have two important design problems: one is aimed at the chemistry of the materials, the other is electronic in nature (when overloaded, it can cause permanent damage and relative overheating). Therefore, it is important to have a battery management system to provide protection and power control. The monitoring system essentially represents the “brain” of a battery pack; it measures and reports information critical to battery operation and protects it from damage over a wide range of operating conditions. The battery management system is a critical factor in electric mobility. The addition of wireless connectivity makes it very attractive but requires a lot of attention. This technology is aimed at sustainability, not only because it eliminates wiring, but also in terms of manufacturing complexity. It also allows you to design the battery pack in a modular and scalable way, so that when you switch to the second life, you can take those packs and tailor them to a specific application and then reconfigure them in a way that suits its second life. In addition to the advantages in terms of weight and flexibility, wBMS also allows for a different way of designing a battery pack. Data acquired through continuous health calculations at the cell and battery module level can be used to determine the residual value of the battery pack more accurately as it enters its second life phase.
In addition to calculating the accumulation of electric charge as a performance parameter, the monitoring guarantees a long battery life and avoids situations that could damage the cells and the electric vehicle itself. The BMS manages the entire array of lithium cells (single cells or entire battery packs), determining a safe operating area, or a safety area within which the battery pack guarantees the best technical and energy performance. The BMS is basically an electronic system for the complete control of all the diagnostic and safety functions for the management of the on-board high voltage and the balancing of the electric charge. The wBMS includes all essential hardware and software parts for power, battery management, RF communication and module-level security functions on a single chip. The main features of an electric vehicle battery management system can be summarized in the following points: battery protection to prevent operations outside its safe operating area, battery monitoring by estimating the state of charge (SOC) and health (SOH) during charging and discharging, and battery optimization thanks to the balancing of the cells which improves their duration and capacity, thus optimizing the driving range for e-mobility vehicles.
Electric cars are becoming popular, with their eco-friendly features in terms of quality, functional simplicity and, above all, energy efficiency. The functional drive is offered by the electric motor whose construction is simple compared to the internal combustion engine. In terms of energy efficiency, the comparison between combustion cars and electric cars is emblematic: the combustion car has an energy efficiency of 16% while the electric one has an energy efficiency of 85%. The electric nature of the propulsion has an advantage over that based on combustion: energy regeneration. Electricity offers a lot of flexibility, including the use of various forms of energy harvesting that help recharge the battery and thus prolong the operation of the vehicle itself. Energy harvesting technologies are therefore at the forefront of the research and development scenario for electric cars.
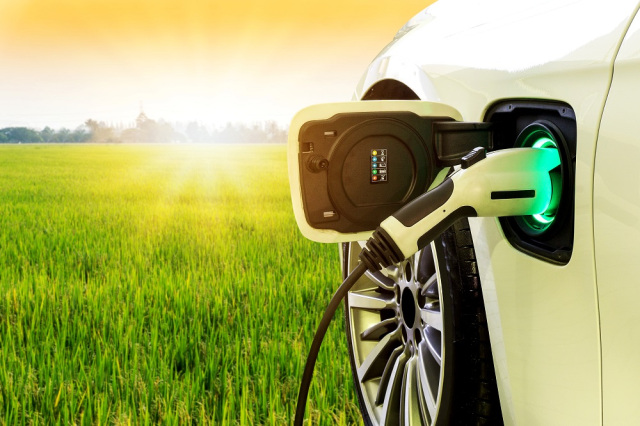
The range of an electric car directly reflects the efficiency of its engine and its energy management system. In addition, the necessary infrastructures, such as the powerful fast charging systems that now reach the power of several hundred kilowatts, are also required to comply with strictly pre-established size and efficiency limits. Due to its specific physical properties, silicon carbide (SiC) represents a valid response to these new market needs. The need to set up charging stations with a compact and efficient design is common to all fast charging systems, and the current SiC power modules allow the creation of systems with the required power density and efficiency. The higher breakdown voltage of the high hardness SiC substrate allows the use of thinner base structures. This allows to reach a tenth of the thickness with respect to the epitaxial layers of silicon. The trend for batteries is to increase their capacity and this feature is associated with shorter charging times.
One incredibly interesting area involves wireless charging of electric vehicles, using charging stations located in garages or public parking lots. Charging points do not necessarily have to be aligned with accuracy with the receiver under the car (as happens with smartphones). In the long term, we will try to develop a version that will allow the integration of long load plates on public roads, in order to load EV/HEV vehicles even on the move, but this will depend on the number of difficulties encountered at the national and local administrative level. Wireless charging technology must be incorporated not only in the vehicles themselves but also in the domestic and urban infrastructure where vehicles are recharged. Wireless charging based on magnetic resonance technology allows electric vehicles, regardless of type or size, to charge automatically and safely by placing the flexible coil on a source pad, using materials such as concrete and asphalt. In wireless charging, the coils used in the power supply are wound separately. A magnetic field is created from a precisely defined frequency (between 105 kHz and 205 kHz) via the coils in the transmitter modules. The coils in the receivers generate a voltage that charges the device’s battery.
Even though they are quieter than internal combustion engines, it would be wrong to assume that electric motors are completely quiet. The noises come from the various components of the engine, such as the inverter and the DC/DC converter. Although electric motors represent a lesser challenge than traditional motors, more effort is still required to develop strategies for mechanical and acoustic insulation. At the same time, there are regulations and strategies to generate noise when the electric vehicle is moving at low speed, representing a danger for the pedestrian who does not hear its passage. When you first cross the street, the first thing you use is your ears. As all vehicles become quieter, the lack of outside noise poses a danger to pedestrians. At typical city speeds, the wind noise is still minimal and engine noise is mostly masked by road and tire noise. Changes in weight distribution, the combination of heavy battery packs and lighter vehicle structures make it difficult to mitigate overall noise.
What about hydrogen cars?
The universal goal for new generation vehicles is a car that produces fewer harmful substances and less noise. The whole world is experimenting with electric vehicles (EVs). One of the disadvantages of electric vehicles, which belong to the electric mobility sector, is that they have long charging times. This is a problem that could be solved with hydrogen. Hydrogen cells harness the same energy used by spacecraft to reach Earth’s orbit. But how do hydrogen cars work? What are the strengths and weaknesses?
Hydrogen vehicles convert chemical energy into mechanics. Hydrogen can burn directly in an internal combustion engine and, in this case, we have a vehicle with a hydrogen internal combustion engine called HICEV. Or it can be used to cause a reaction with oxygen in a fuel cell, thus producing electricity. This type of vehicle is called FCEV (fuel cell electric vehicle) and, in recent years, FCEV has attracted the attention of many manufacturers. The FCEVs are powered by an electric motor and have an on-board power plant to allow the production and management of hydrogen. The environmental impact of hydrogen-powered cars is minimal as they do not generate polluting emissions (greenhouse gases, fine dust, and so on), but only water vapor. Hydrogen is the most abundant chemical element in the universe, but not in natural form. For this reason, it is not exactly a renewable source and must be produced with different systems. The overall environmental impact depends on the energy source used to produce it. The use of renewable sources will reduce it to a minimum.
Hydrogen can be produced through two different production processes and technologies: reforming and electrolysis. The first has a greater environmental impact because it involves the extraction of crude oil, transport, and refining. Electrolysis is the process of splitting H2O water molecules into individual hydrogen and oxygen atoms through the chemical reaction induced by electricity. This production process does not emit polluting gases but requires a large amount of energy. The electrolysis process consists of a low voltage current that flows through the water to release oxygen and hydrogen in gaseous form.
Hydrogen makes an essential contribution to the sustainable mobility of the future together with battery powered cars. FCEV cars may represent zero-emission technology, but we still need to improve hydrogen production through renewable solutions. It is essential to reduce infrastructure costs for transportation and distribution. The same goes for electric charging infrastructures. The goal is to reduce the environmental impact on electric charging.
This article was originally published on EE Times Europe.
Maurizio Di Paolo Emilio holds a Ph.D. in Physics and is a telecommunication engineer and journalist. He has worked on various international projects in the field of gravitational wave research. He collaborates with research institutions to design data acquisition and control systems for space applications. He is the author of several books published by Springer, as well as numerous scientific and technical publications on electronics design.